Profimach® Specialist in Deep Holes Machines
High quality affordable deep hole drilling- and boring machines
Our high precision deep hole drilling machines, BTA and gundrilling machines, SRB Machines, Honing Machines, Boring and Counterboring machines have been specially developed and improved in recent years with tthe help of several famous European and Japanese machine tool builders.
All essential castings are made oversized of high grade of cast iron that is stress relieved through annealing to eliminate internal stress. With the greatest stiffness and stability of the castings, our machines are suitable for a lifetime of precision deep hole working.
Our deep hole working machines are offered
with a full two-year limited warranty.
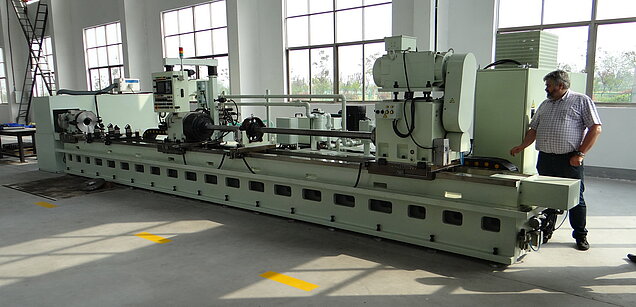
Best SRB Machines available in the Market!
Japan Technology combined with European Quality awareness
What deep hole machining do you have in mind?
Deep Hole Machining Processes our machines can do:
Gun Drilling
Gun Drill Proces
Gun drilling process is used to produce deep and straight holes. This process is very specialised as compared to the conventional twist drilling process. The standard gun drill tool geometry has a single effective cutting edge. Unlike the twist drill the gun drill cuts through the metal eccentrically and once inside the component the tool self-pilots itself. The hole is further burnished due to the guide pads which finally results in a precise round hole with maintained straightness. The Coolant enters the tool through the coolant through hole and the chips are gushed out through the V shaped profile on the gun drill. Gun Drilling is effective from ф1 to ф30, but if you wish to go higher, BTA drilling becomes more effective than gun drilling.
Gundrilling, one of the basic and frequently performed material removal processes in the automotive, die and mold, and turbine industries, is becoming increasingly more complex, demanding, and experiences an unprecedented growth. Inspite of significant increase in the demand for economically producing holes and forprocess reliability, gundrilling and gundrill manufacture are still considered an esotericart, and there still exists a lackof knowledge on the exact relationships between the point geometry, the grinding process parameters, and the process mechanics, resulting inmany methods for drill production and, consequently, in wide variations in process performance.
BTA drilling: Drilling, Boring and Trepanning
BTA drilling Process : Drilling, Boring and Trepanning
BTA stands for Boring and Trepanning Association which developed this deep hole drilling system. It involves a single drill tube in which high pressure coolant is supplied to the drill through the annular area between the drilled hole and the tube outer diameter. The chips are evacuated through the I.D. of the tube. The drill head is screwed to this drill tube which is much stronger compared to the kidney shaped shank of a gun drill, hence much higher metal removal rates are possible. This involves the use of a Pressure head which is basically a high pressure seal between the workpiece and the drill bush. BTA/STS drilling is generally used for ф19 and above.
Since the chip removal is internal, no v shaped groove is required in the shank, so its cross-section is completely round and this provides more rigidity to the entire system. BTA drilling finds its application in Industries like Oil & Gas, Defence, Steel, Aircraft, Aerospace, Hydraulic Cylinders, and Power etc. For larger diameter deep hole drilling, BTA drilling is the only available option which provides high productivity and precision.
Another system which evolved from BTA single tube system is the Ejector drilling system. It is a system with twin tubes where the coolant is pumped through the space between the inner and outer tube. This eliminates the use of Pressure head and simplifies the system. This was introduced mainly to tool up conventional machines to do Deep hole Drilling.
Trepanning
Trepanning Process is done on standard BTA drilling/boring Machines
Trepanning is a special operation mainly used on when conventional machines are tooled up to do deep hole drilling. Usually in such cases the machine power is less and hence Solid BTA drilling is not possible. Trepanning is also used when a solid core is required. The trepanning operation is performed on a blank workpiece without any holes. The Tool geometry allows cutting only on the circular section whereas a solid core is left in the middle. This core can later be extracted for use. Typically only through hole applications are advisable with Trepanning since the core extraction can become troublesome in case of a blind hole. The tool covers a large range of diameters upto 500mm. There are limitations to the lower level of diameter that can be achieved with this process due to the geometry of the tool.
Go to our Trepanning and Boring/Drilling Machines
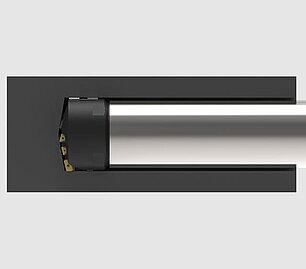
Ejector Drilling
Ejector Drilling Process
Ejector Drilling is similar to BTA Drilling operation with the difference that it has Twin tubes instead of a single tube.The high pressure Coolant is pumped to the cutting face through the annular area between the outer tube and the inner tube. There is a special connector for holding both the tubes and also to feed the high pressure coolant.The pressure head with rear coolant sealing that is required in BTA drilling is eliminated here and only a guide bush is needed.The Chips generated are evacuated through the inner tube where ejection effect is generated at the rear end to help in chip evacuation.The area for chip discharge is comparatively less than BTA and hence the evacuation is not as efficient particularly in smaller sizes. Since the tube diameter is larger than BTA Drilling the torsional strength also goes up. This can be an advantage to go for higher feeds. This is usually used to retrofit conventional machines for deep hole drilling.
Goto our Ejector drilling Machines
SRB - Skiving Roller Burnishing
SRB - Skiving Roller Burnishing Process
Skiving is a hole finishing process used when very tight dimensional and geometrical tolerances are required. It is the fastest method to achieve surface finish having very fine peaks and valleys ideal for roller burnishing process. The Skiving Tool is basically a twin/multiple edge floating reamer which follows the existing bore. The Roller burnishing tool coldworks the surface by merging peaks & valleys thereby producing very high surface finish and also a hardened surface. Both Skiving and Roller burnishing processes can be done simultaneously by using combined Skiving cum Roller Burnishing Tool. This process is 8 – 10 times faster than honing operation. The Skiving blades and burnishing rollers are expanded hydraulically while rotating and feeding though the bore. At the end of the operation these are retracted and the tool is withdrawn. High pressure coolant is supplied to the tool through the annular area between the bore and the tube outer diameter. The coolant along with the chips is evacuated from the other side.
Profimach offers dedicated Skiving & Burnishing machines for high production scenarios. This setup can be accommodated in a BTA drilling machine.
Honing
Honing Process
Honing is a process that uses Silicon Carbide , Aluminum Oxide, CBN or Diamond tools to polish the ID of a cylindrical shaft . These tools are mounted on a mandrel that is rotated and reciprocated at the same time. Expansion of the mandrel is controlled by servo controls or hydraulically. Honing gives a surface finish of 0.1 Ra or better in most cases.
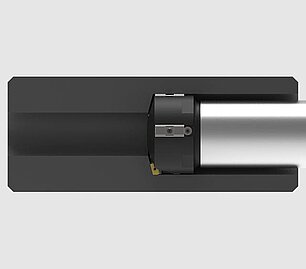
Counter Boring
Counter Boring Process is done on our Standard BTA Drilling/Boring Machines
Counter Boring operation basically enlarges a pre-drilled bore. Usually counter boring is used when machine power does not allow solid drilling of that size.It covers a large range of diameters up to 500mm. The number of cutting edges on the tool can vary depending upon the amount of stock removal. As the counter bore tool enters the component, the pads are supported by the finished bore diameter. The Coolant and chips flow is similar to BTA drilling operation or chip forward.
Bottom forming
Bottom Forming Process is done on our Standard BTA Drilling/Boring Machines
Gun Drilling and BTA drilling operations usually leave the bottom of the hole with a “W” Shaped profile. Bottom forming is a process that is basically used to generate a flat bottom or a profiled end for a pre-drilled hole. It’s an operation to finish the end of the hole. The desired end can be generated for example Flat bottom, steps, radius etc.
Goto our Standard BTA Drilling/Boring Machines for Counter Boring Process
Pull Boring
Pull Boring Proces can be done on our BTA boring Drilling Machines
Pull boring is being used mainly to have very straight and accurate long holes. The oil is fed similar to BTA drilling or counter boring i.e. through the pressure head. This has guide pads which are supported in the pre-bore, thus producing the enlarged bore on the original axis.
Bottle boring Process
Bottle boring Process can be done on our standard BTA drilling/boring Machines
Bottle boring is mainly used for generating internal profiles in pre-drilled bores.The Tool design allows for the expansion or retraction of the cutter when actuated from rear end. This can be used to produce the required internal profile in the work piece. Bottle boring tools are developed for specific internal profiles of components. The internal profile is larger than the tool entry and exit diameters. The operation requires the use of CNC controls to program the various coordinates for the required profile.
Goto our BTA Boring/Drilling Machines for bottle boring operation
Pull Reaming
Pull Reaming Process can be done on our BTA drilling boring machines
Pull reaming is used to improve straightness and accuracy of long holes. The reaming tool is rotated and pulled through the drilled hole. The surface finish as well as size of drilled hole is improved using this process. Profimach provides reliable, well designed machines for this process that are guaranteed to perform.
Deep hole drilling
There are three traditional deep hole drilling methods: gundrilling or single lip drill system, BTA or single tube system (STS) and ejector Sytem or double tube system (DTS).
Gun Drilling
Single Lip Drill System
SLS
Ø 2~40 mm
BTA Drilling
Single Tube System
STS
Ø 20~1400 mm
Ejector Drilling
Double Tube System
DTS
Ø 20~500 mm
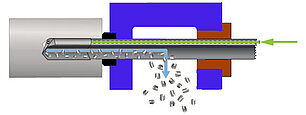
Gun drilling
Gun drilling is the oldest and most widely used method of deep hole drilling employed by industry today. The drill or “gun drill” is generally a one-piece assembly consisting of a hollow cylindrical drill driver. Also, it is brazed to a V-shaped crimped tube and finally assembled to a brazed-on solid carbide drill head. Both the crimped drill shank and the brazed-on carbide drill head from a kidney-shaped cross-section. Whereby the open V-shaped section acts as a chip flute.
Gun Drilling Systems Features
In all cases, gun drills require filtered, the high-pressure coolant that is introduced through the center of the crimped gun drill shank. Then the drill is directed to a coolant orifice in the carbide drill head. The high-pressure coolant provides lubrication for the drill head. Also, this assures that all of the chips produced by the drill head are exhausted through the V-shaped chip flute of the gun drill shank. Gun drilling is better known as an internal coolant supply / external chip exhaust method of drilling.
Gun drills are generally used on single purpose gun drilling machines as well as on a variety of machining. They have turning centers that are equipped with sufficient high-pressure coolant and filtrations systems. With this system of drilling, one can expect to drill to depths in excess of 100 x dia.
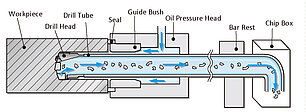
BTA: Single Tube Systems - STS
The single tube system STS or sometimes referred to as the “BTA” system of drilling, is the reverse of a gun drilling system. Unlike the gun drill, the STS or “BTA” drilling system assembly consists of a drill head that is attached to a ground cylindrical tube. This is by either an internal or external fast lead thread. The drill tube or boring bar is smaller in diameter than the drill head which forms an annular space between the hole being drilled and the OD of the drill tube or boring bar. This space is known as “oil room” and in conjunction with a coolant induction unit or a pressure head. In addition, it makes it possible to direct filtered high volume coolant to the drill head cutting edge.
Single Tube Systems Features
This pressure head seals against the entry side of the part to be drilled. Also, this directs the coolant to the detachable drill head. The coolant provides lubrication for the drill head and assures that all of the chips produced by the drill head are directed through the detachable cutting head are flushed internally through the ID of a cylindrical hollow drill tube or boring bar. This is better known as an external coolant supply / internal (ID) chip exhaust method of drilling.
The STS / BTA system supports tools ranging from 12 mm – 850mm diameter. These tools and this system allow depth to diameter ratios in excess of 100 x’s dia. In most cases, the STS / BTA system is set up on dedicated deep hole drilling machines. This system is the best choice for extremely deep bores. And, for materials with poor chip forming properties such as stainless steel, Titanium, and low carbon steel.
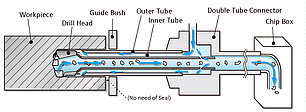
Double Tube System - DTS
The double tube system, DTS, also referred to as the Ejector system, is characterized by two tube construction. It consists of an outer and inner tube connected to a coolant inducer at one end and a drill head at the other by a four-start thread.
How does it work?
The pressurized coolant is introduced by the coolant connector to flow through the annular space between the two tubes, the inner and outer, towards the drill head. Most of the coolant flows through holes in the drill head therefore providing lubrication and chip evacuation within the inner tube of the system. Also, the remaining coolant is directed through the rear of the inner tube. This creates a partial vacuum in the inner tube that sucks the coolant and the chips from the drill head through the inner tube before transferring it to a chip exhaust port that is an interracial part of the coolant connector.
Double Tube Systems Requirements
Double Tube Systems do not require a sealing system and pressure head, unlike the less powerful Single Tube System. The DTS system can be used on conventional machine tools such as lathes, horizontal boring mills and machining centers which have suitable feed mechanisms, rigidity, and our self-contained coolant system. The DTS has more applications than it’s single tube counterpart.
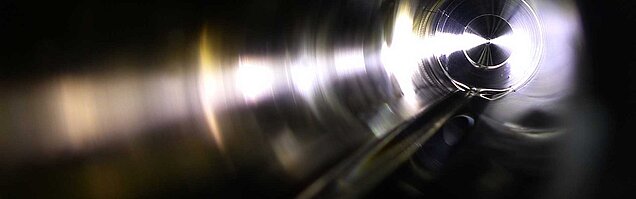
Deep hole machining - Deep hole cutting solutions, Gundrilling machines, Deep hole drilling machines,- BTA drilling machines ,- SRB Machines ,- Micro drilling machine - Mold drilling machine - Table type drilling machine Overview Deep hole machining, Deep hole drilling - Gundrilling - BTA - Trepanning, Single coordinate single spindle CNC Gundrilling Machines, Single coordinate multi spindle CNC Gundrilling Machines, Three coordinate single spindle deep hole driling machine, Deep Hole Drilling and Boring Machine - BTA Boring and drilling machines, Trepanning Machines or Big diameter Boring machine - Big diameter BTA machine, SRB - Skiving & Roller Burnishing Machines, Deep hole burnishing - roll-finishing - roller burnishing, Deep Hole Honing Machine, Bottom forming drill machine,PROFIDRILL PDDV-HS : High speed Vertical Deep hole drilling machines, Deep hole drilling Technology, Deep hole drilling accesoiries, Profimach, Profidrill, Deep hole machines, Deep hole cutting solutions, Gun drilling machines, Deep hole drilling machines, BTA drilling machines, Deep hole boring and drilling machines, deep hole boring machines, SRB Machines, Skiving Roller Burnishing Machines, Deep hole honing Machines. Single tube deep hole drilling system STS, double tube deep hole drilling system DTS, Micro drilling machine - Mold drilling machine - Table deep hole drilling machine, reverse boring machines, pull boring machines,