SRB: SKIVING ROLLER BURNISHING OF TUBES
THE MOST MODERN, MOST EFFICIENT, FASTEST AND MOST ECONOMICAL PROCESS TO RAPIDLY FINISHING THE INTERIOR TUBE DIAMETER (ID) FOR HYDRAULIC CYLINDER APPLICATIONS
Skive and Roller Burnishing is a modern process to rapidly finishing the interior diameter (ID) of a tube
to a hydraulic cylinder quality size and finish.
The production technology of skiving and roller burnishing is used for the manufacture of cylinder tubes. Among other aspects, the cylinder construction industry places great emphasis on resistance to internal pressure, such that the loss in customization can be kept as low as possible. Of course, the focus of attention is on the quality of the bore. Here, the requirements of the piston seals are decisive for the required values of the surface roughness and diameter tolerances. Skiving reduces diameter deviations and ovality caused by the raw stock. The rolling, which takes place in the same process, ensures the required internal diameter tolerances and asperity values.
Extensive series of tests by the well-known seal manufacturers have recognized rolling or even smooth rolling as a suitable production process for the seal running surfaces. However, the cost aspect is equally as important as the quality. Here, the great advantage of skiving and roller burnishing is in the rapid production of the tubes, which primarily reduces the price compared with honing. A further advantage of skiving and roller burnishing is in the long manufacture lengths that can be produced.
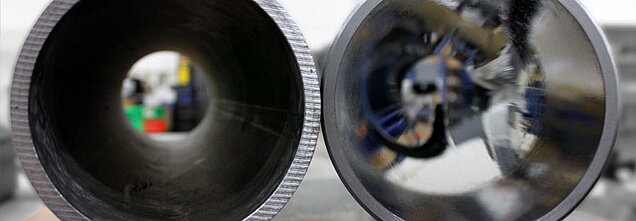