Deep hole processing
Deep Hole Technology
What is Deep Hole Drilling?
A deep hole is defined by its depth-to-diameter ratio (D:d),
and typically holes greater than 10:1 are considered deep holes.
Deep hole machining means machining of holes deeper than ten times the hole diameter. This can be done in different machine set-ups. The most common method is rotating the work piece while the tool is fed in a linear movement. Rotating tool is another option as well as a combination of the two.
Deep hole machining is generally performed on dedicated deep hole drilling/boring machines which are manufactured and assembled to optimize the processes for straightness and efficiency. Advances in technology allow our highly capable BTA and gundrilling machines, produced under OEM, with applications exceeding depth-to-diameter ratio of 400:1.
Deep hole drilling consists of BTA drilling (boring) and gun drilling, with additional processes designed for specific tolerance objectives and generally performed on BTA-style deep hole drilling machines. Deep hole machining is used in a variety of materials from aluminum to super-alloys, and is capable of achieving tight diameter control, straightness, and superior surface finish into workpieces. Deep hole drilling processes work by using special tools and setups to deliver high pressure coolant, evacuate chips cleanly, and achieve depth-to-diameter holes into metal beyond what a common CNC machine can reach. This allows manufacturers to achieve their manufacturing tolerances and production requirements reliably, accurately, and efficiently.
Regardless of method, the basic principles of drilling still apply, and the correct choice of cutting speeds and feeds are crucial. Satisfactory chip breaking, and removing the chips from the cutting edge without damaging the tool or work piece, is essential. One of the most important success factors is an effective coolant system.
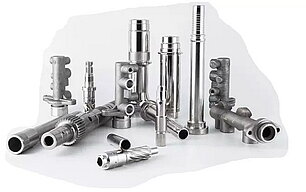
Holes are important surfaces on boxes, brackets, sleeves, rings, and plate parts, and are often encountered in machining. If the machining accuracy and the surface roughness are the same, the machining of the hole is more difficult than the machining of the outer circular surface. The productivity of the hole drilling is lower but the cost is higher.
Because the size of the drilling tool is limited by the size of the hole to be machined, the rigidity of the tool is poor. The machining with a large cutting amount also cannot be used. When the hole is machined, the cutting area is inside the workpiece, and the cutting fluid is not easy to enter the cutting area, chip removal, and heat dissipation. The machining accuracy and surface quality are difficult to control in poor conditions.
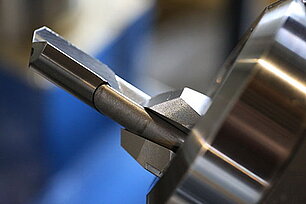
The processing method of the hole includes drilling, reaming, boring, broaching, honing, skiving, etc. In addition, there are some special processing methods like trepanning drilling, electric discharge machining (EDM). Different tools are selected based on different materials, sizes, and precision requirements. Also, different processing techniques are according to different efficiency requirements, quantity, and ratios of length/diameter. In the mechanical manufacturing industry, a cylindrical hole having a hole depth exceeding 10 times the diameter is generally referred to as a deep hole.
Deep hole machining is a type of machining method that is dominated by specially designed tools. These special tools feature extended, high-precision shanks with support and integrated reamer. Besides, they combined with the latest cutting edge geometry, special tool material, efficient coolant and chip control. So the workpieces with high quality can be stably produced by maximum penetration.
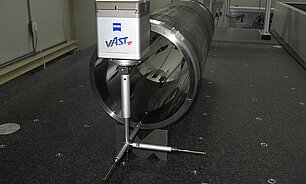
Operating points during deep hole machining
1. The concentricity among the spindle, the tool guide sleeve, and the tool/the workpiece holder support sleeve should meet the requirements.
2. The shape of the chip should be kept normal to avoid the formation of straight strips.
3. When using the drill with a higher speed to machine and nearly finish the through-hole, it should be slowed down or stopped to prevent damage to the drill bit.
4. A lot of cutting heat will be generated during deep hole machining, and it will not dissipate easily. It is necessary to supply sufficient cutting fluid to lubricate and cool the tool. The cutting fluid system should be also unblocked and normal.
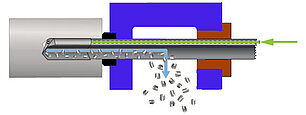
Difficulties of deep hole processing
1. The cutting condition cannot be directly observed. It only can be judged by listening to the sound, looking at the chips, observing the load of the machine tool, and the parameters of oil pressure.
2. The heat by cutting is not easy to dissipate.
3. Chip removal is difficult. If the chip is stuck, it might cause damage to the drill bit.
4. Due to the long length of the drill rod, poor rigidity and easy vibration, the axis of the hole is easily deflected, which affects the processing precision and production efficiency.
Chip Control, chip control and more chip control
and chip control
Deep hole drilling comes down to chip control. Cutting metal is cutting metal, even if you can’t see the tool or the chip. The critical part of deep hole drilling is getting the chips out of there. Different technologies have been developed to take care of accurately cutting the metal and effectively evacuating the chips. If you don’t get the chips out of there you’ll ruin the tool and the part. If even one chip gets stuck in the drill throat or elsewhere, it can cause a logjam of chips. The drill heats up, the piece is ruined and you have to take out the drill and dig out the chips.
At startup on a new part, or even a new piece, the operator must start with the recommended feed and speed. Meanwhile, the operator stationed by the chip exhaust port catches chips in a strainer. Depending on what the chips look like the operator makes small adjustments to produce chips that will flow well, increase feed or reduce rpm if the chips are too long, or increase the rpm to thin out the chip.
So chip control is critical, and for every part you have to dial in the feed and speed to make the chips the right size and shape. Small changes in feed and speed can mean the difference between success and disaster.