The future of the auto industry is interesting but uncertain
No one knows how quickly electric vehicles are going to replace gasoline- and diesel-powered vehicles, how completely it will happen.
However, we do know that fuel economy standards continue to progress and drive vehicle design toward smaller displacement, higher-technology engines. As a result, technology that was developed years ago for high-performance vehicles is now becoming mainstream. For example, sodium filled valves, which formerly were used in only extremely high-performance engines to manage heat in the valve train, are becoming more common. The same goes with hollow camshafts, which reduce energy-consuming rotational inertia and provide opportunities for engine management.
Within vehicle drivetrains, today’s automatic transmissions now have as many as eight or even 10 speeds instead of five or six. This wide selection of gear ratios enables smaller displacement engines to provide better fuel economy and deliver higher performance.
These kinds of technological upgrades for higher performance and economy are not new, but previously were considered too costly for general use. Now, advanced manufacturing and materials technology make common application of these upgrades viable.
Enabling Cost-Effective Production of high tech Car valves
Deep hole drilling is one advanced manufacturing technology that allows for the cost-effective production of key features of those performance-boosting parts. Sodium-filled valves, for example, have holes drilled the length of the valve stem in which liquid sodium circulates and draws heat from the valve head. Precise deep hole drilling methods enable hollow and more energy-efficient camshafts to be manufactured. Complex multi-speed transmissions feature shafts with multiple off-center holes of varying depths for lubrication or hydraulic sequencing. The holes in the shafts are too deep to produce effectively on machining centers, so deep hole drilling machines are critical in those instances.
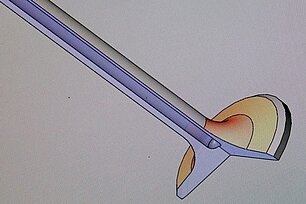
Engineers can also play with the margin on the valve to help reduce weight.
Hollow-stem valves can offer up to 25 percent weight savings over similar traditional stainless-steel counterparts.
Engine builders are looking at hollow-stem valves as a way to reduce weight and increase rpm without switching to costly titanium valves.
Hollow stem engine valves are making a comeback. It’s been hitting the market hard in the last five years, due to the weight savings and RPM gains. Also, the overall stress levels of the spring decrease anywhere from 20 to 30 percent.
Much of the emphasis on valvetrain performance in recent years has focused on stiffening the pushrods and rocker arms, correcting the geometry and improving the fatigue life of the valve spring. Engine builders then challenged those improvements with more aggressive camshafts, and lighter valves helped not only with acceleration rate but also increasing redline. But with deep hole drilled hollow engine valves you can see from 300 to 600 rpm gains just from switching to hollow stem valves.
