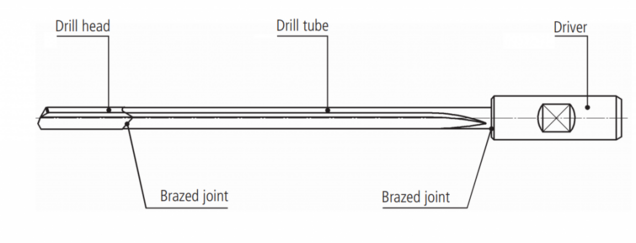
Machining knowledge of gun drilling
Deep hole gun drilling basic knowledge
Deep hole gun drilling, also called deep hole drilling. Originally applied to weapons manufacturing industry, drilling of guns, hence the name of gun drill, along with the continuous development of science and technology of deep hole machining system manufacturer's unremitting efforts, the deep hole processing has become a convenient and efficient processing method. And is widely used in such as: automobile industry, aerospace industry, structure building industry, medical equipment industry, mold, tool, fixture, industrial and oil pressure air pressure industry etc..
Gun drill is an ideal solution for deep hole processing, the use of the gun drill can obtain a precision processing, processing by the hole position precision, linearity, high coaxiality, and has the very high surface finish and tiny deviation. Capable of deep hole convenient processing of various forms of. In practical application, through a first hinge processing instead of processafter drilling, but also has very strong reliability technology.
The gun drill can drill cast iron, carbon steel, copper, aluminum alloy, alloy steel and so on. The hole will be finished drilling, boring, and reaming once completed. The drill bit can do processing of high precision (grade IT8-11), fine linearity (0.16-0.5mm/1000mm) and low roughness (Ra6.3-Ra0.8)hole.
The drilling bits can handle speed of 30-100 M / min or more.
Gun drill is mainly used for drilling holes diameter range is greater than in 1.5mm-40mm, the ratio of length to diameter of drill bit diameter X150 times
Gun drill instructions
Basic instructions to use a gundrill efficient!
- You must first select a size suitable for the guide sleeve, the guide sleeve head and gun drill clearance is maintained within 0.003mm--0.008mm.
- The gun drilling machine using the gun drill must have high axial and radial stiffness in the spindle, the guide sleeve and the spindle must have high precision in axiality.
- In the process of drilling, when material is processed (especially casting), the drilling position should not be on a fracture, porosity and other impurities, otherwise it will cause chipping, and even turn around.
- The correct selection of the cutting parameters is extreme important for a good result. The cutting speed under normal circumstances: V=1.1-1.65 M / s, the amount of feed: s=0.015-0.03mm / rev, oil pressure: P=2.5-6.0 Mpa, flow: Q=0.2-0.65 L / s.
- Gun drilling cutting fluid used is also very important, it directly affects the accuracy of themachined hole. Be sure to choose a special gun drill for oil. General gun drill used cutting fluiddue to extreme pressure additives, in order to ensure the oil film formed under high pressure,prevent dry grinding.
- Viscosity and diameter of drill cutting fluid is concerned, the smallerdiameter, the lower the viscosity. Compared to cutting oil gun drill cutting area and the general mechanical processing has the characteristics of high pressure, large flow, high filtering precision. Flow rate should be increased with the increase of pressure, in order to ensure cutting oil has a greater flow rate, to achieve the purpose of smooth chip removal.
- the gun drill bit wear: the need for timely correct edge grinding is important for straight holes
- The edge can be regrinded on the universal cutting tool grinder we also provide. Our Gun drill grinding machine you can find here.
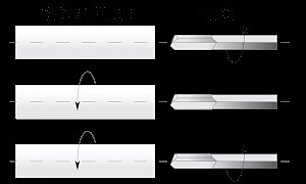
Deep Hole drilling can be performed in 3 manners:
- Rotating tool, stationary workpiece
- Rotating workpiece, stationary tool
- Counter rotating tool and workpiece