BTA drilling machines feeding drives
Ballscrew drive or Pinion and Rack drive
BTA Drilling Machine with Ball-screw feeding system
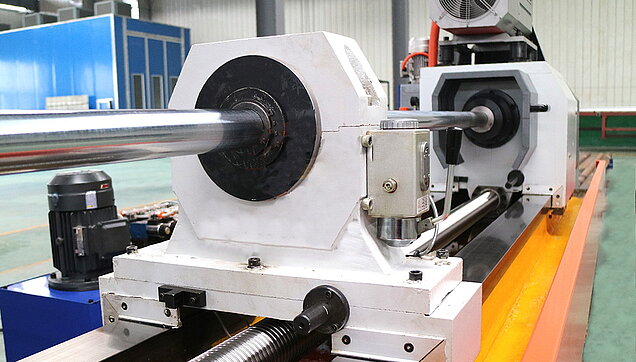
BALL SCREW DRIVE SYSTEMS
Ball screw. What is it?
Made up of a nut, screw, and ball bearings, ball screw drive systems work like typical power screws but the rolling friction replaces the sliding friction. As the screw rotates, the machine moves.
What does it do well?
When done correctly, ball screws have exceptional accuracy and are friction-free, sliding smoothly with the motion. There are also more mounting options. Racks have to be bolted to something for their entire length, where ball screw may be a better fit for some machine designs. Ball screws systems are also easier to use in the manufacturing process, where rack and pinion may require more processes to be built correctly.
What are its weaknesses?
As stated above ball screws are known for being accurate and friction-free. However, on a longer axis, vibration can worsen as increased speed is needed, hence making the screw rotate faster. This issues is coined as “screw whip”. A ball screw driven system may need bigger motors or more gearing compensation for “screw whip” and to maintain machine positioning speeds, making the use of a ball screw on axis over 1500mm in length not ideal. Ball screw systems are best suited for height positioning or the Z axis because of the short travel distance.
In regard to speed, ball screws cannot accelerate as quickly nor can they maintain the higher speeds as efficiently. Their stiffness is lower and less constant. Their transfer of power, or efficiencies, is in the 80-85% range.
Serviceability is also trickier with ball screw systems, usually requiring specialized skills to replace which isn’t ideal being that ball screws can be very sensitive. Ball nuts are very sensitive to misalignment, especially when opposing nuts are used. Ball screws are also more susceptible and less forgiving to contamination and harsh environments (like stone shops) which can lead to catastrophic failures.
BTA Drilling Machine with Pinion and Rack feeding system
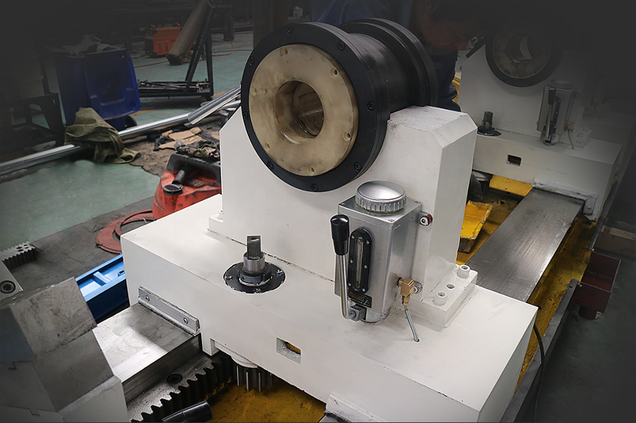
RACK AND PINION DRIVE SYSTEMS
Rack and Pinion. What is it?
A rack and pinion drive system is just what it sounds like. There is a rack that is bolted onto the sides of the machines and pinion, or cog/gear, that meshes with the rack. As the pinion turns, the machine moves. Straight racks and helical (angled) racks merge to drive.
What does it do well?
Best known for their rigidity, rack and pinion drives can deliver precise motion over unlimited lengths. They are built to travel the full distance of a machine, no matter the length, without “screw whip” concerns (more on that later). Rack and pinion systems have high up-time and can produce for years with minimal wear and are very favorable in the environment of a fab shop, being virtually impervious to dust and debris.
Helical rack and pinion designs are angled instead of straight, with more teeth in the mesh of the rack. The helical design creates a smooth, low-friction movement and delivers zero backlash with a positional accuracy of ±0,005mm throughout the entire travel distance of the machine. They also excel in accelerating, de-accelerating, and maintaining higher speed processing which is a result of their constant stiffness and exceptional transfer of power, or efficiencies, that are upwards of 97%.
The simplicity in the design of rack and pinion is a huge plus, benefiting end users. They are usually simple bolt-on systems that are easy to replace – not requiring special skills or knowledge.
What are its weaknesses?
Old rack and pinion technology was known for their cons of having higher friction and potential backlash of the pinion. Advances in gear production techniques (milling, grinding, and heat treatment, for example) have dramatically improved the precision and load carrying capacity of rack and pinion drives, to the point that they are a competitive component for any linear-axis drive application.