Profimach® STS Deep Holes drilling Machines
High quality affordable deep hole machines
These high precision deep hole BTA drilling machines (STS: Single Tube System) have been specially developed and improved in recent years. All essential castings are made of high grade of cast iron that is stress relieved through annealing to eliminate internal stress. With the greatest stiffness and stability of the castings, these machines are suitable for precision deep hole working.
These deep hole BTA machines are offered with twofull-year limited warranty .
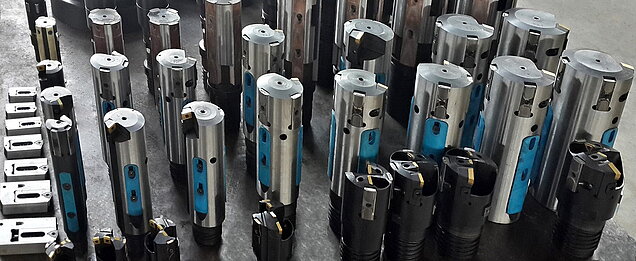
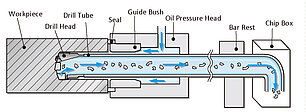
BTA: Single Tube Systems - STS
The single tube system STS or sometimes referred to as the “BTA” system of drilling, is the reverse of a gun drilling system. Unlike the gun drill, the STS or “BTA” drilling system assembly consists of a drill head that is attached to a ground cylindrical tube. This is by either an internal or external fast lead thread. The drill tube or boring bar is smaller in diameter than the drill head which forms an annular space between the hole being drilled and the OD of the drill tube or boring bar. This space is known as “oil room” and in conjunction with a coolant induction unit or a pressure head. In addition, it makes it possible to direct filtered high volume coolant to the drill head cutting edge.
Single Tube Systems Features
This pressure head seals against the entry side of the part to be drilled. Also, this directs the coolant to the detachable drill head. The coolant provides lubrication for the drill head and assures that all of the chips produced by the drill head are directed through the detachable cutting head are flushed internally through the ID of a cylindrical hollow drill tube or boring bar. This is better known as an external coolant supply / internal (ID) chip exhaust method of drilling.
The STS / BTA system supports tools ranging from 12 mm – 850mm diameter. These tools and this system allow depth to diameter ratios in excess of 100 x’s dia. In most cases, the STS / BTA system is set up on dedicated deep hole drilling machines. This system is the best choice for extremely deep bores. And, for materials with poor chip forming properties such as stainless steel, Titanium, and low carbon steel.
BTA deep hole drilling is a process that accurately drills holes from 20 – 1250 mm in diameter with higher feed rates.
BTA drilling is a deep hole drilling process that uses a specialized drilling tool on a long drill tube to produce deep holes in metal, from holes with a diameter of 20 mm and larger, up to depth-to-diameter ratios of 400:1. BTA drilling is the most effective method of drilling deep holes, as it is a cleaner, more reliable and capable process than conventional twist drills, and can achieve larger diameters and higher feed rates than the alternative gundrilling.
BTA drilling tool heads are threaded or mounted onto long drill tubes, and use multiple cutting surfaces on a single tool to remove chips efficiently, exhausting them using high-pressure coolant through holes in the tool head, then out the drill tube and through the machining spindle.
BTA stands for Boring and Trepanning Association, and is also sometimes referred to as STS (single tube system) drilling, as it uses one single drill tube for the BTA tool, compared to other processes such as ejector drilling, which use two.
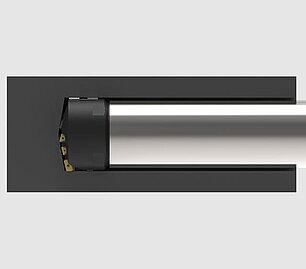
Ejector Drilling Process
Double Tube System - DTS
Ejector Drilling is similar to BTA Drilling operation with the difference that it has Twin tubes instead of a single tube. The high pressure Coolant is pumped to the cutting face through the annular area between the outer tube and the inner tube. There is a special connector for holding both the tubes and also to feed the high pressure coolant.The pressure head with rear coolant sealing that is required in BTA drilling is eliminated here and only a guide bush is needed. The Chips generated are evacuated through the inner tube where ejection effect is generated at the rear end to help in chip evacuation. The area for chip discharge is comparatively less than BTA and hence the evacuation is not as efficient particularly in smaller sizes. Since the tube diameter is larger than BTA Drilling the torsional strength also goes up. This can be an advantage to go for higher feeds. This is usually used to retrofit conventional machines for deep hole drilling.
EJECTOR DRILLING can be build on our standard BTA drilling machines!
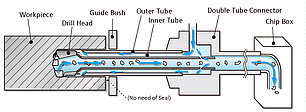
Double Tube System - DTS
The double tube system, DTS, also referred to as the Ejector system, is characterized by two tube construction. It consists of an outer and inner tube connected to a coolant inducer at one end and a drill head at the other by a four-start thread.
How does it work?
The pressurized coolant is introduced by the coolant connector to flow through the annular space between the two tubes, the inner and outer, towards the drill head. Most of the coolant flows through holes in the drill head therefore providing lubrication and chip evacuation within the inner tube of the system. Also, the remaining coolant is directed through the rear of the inner tube. This creates a partial vacuum in the inner tube that sucks the coolant and the chips from the drill head through the inner tube before transferring it to a chip exhaust port that is an interracial part of the coolant connector.
Double Tube Systems Requirements
Double Tube Systems do not require a sealing system and pressure head, unlike the less powerful Single Tube System. The DTS system can be used on conventional machine tools such as lathes, horizontal boring mills and machining centers which have suitable feed mechanisms, rigidity, and our self-contained coolant system. The DTS has more applications than it’s single tube counterpart.
BTA Drilling vs Gun Drilling
BTA drilling can achieve drill feed rates of typically 5-7 times faster than gundrilling
BTA drilling can achieve drill feed rates of typically 5-7 times faster than gundrilling at the same diameter, due to the tool design, more efficient chip exhaust, and machine design and power. BTA boring/drilling is VERY effective in holes from 20 – 350 mm (till 1200 mm we will use trepanning tools), a greater size range than gundrilling. BTA drilling machines introduce coolant around the tool head, and evacuate chips through the center of the drill and through the machine spindle, compared to gundrilling, where coolant is introduced internally through the drill and chips exit through an external groove. BTA drilling is not suitable for diameters lower than 20mm where gundrills take over till less than 2 mm diameter.
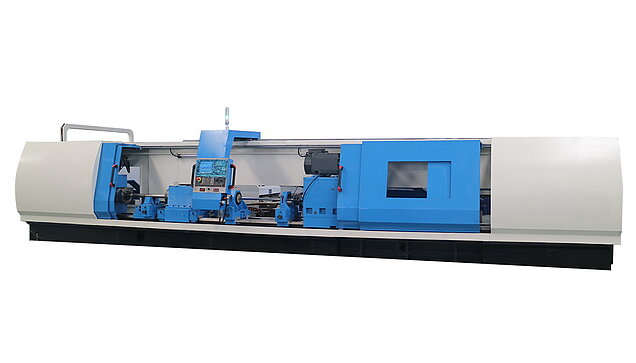
BTA drilling machines
BTA deep hole drilling machines PDHB-100 Series
Boring diameter till 100 mm
BTA deep hole drilling machines PDHB-160 Series
Boring diameter till 160 mm
BTA deep hole drilling machines PDHB-200 Series
Boring diameter till 200 mm
BTA deep hole drilling machines PDHB-360 Series
Boring diameter till 360 mm
BTA deep hole drilling machines PDHB-500 Series
Boring diameter till 500 mm
BTA deep hole drilling machines PDHB-800 Series
Boring diameter till 800 mm
BTA deep hole drilling machines PDHB-1000 Series
Boring diameter till 1000 mm
BTA deep hole drilling machines PDHB-1200 Series
Boring diameter till 1200 mm
BTA drilling machines feeding drives
Ballscrew drive or Pinion and Rack drive
BTA Drilling Machine with Ball-screw feeding system
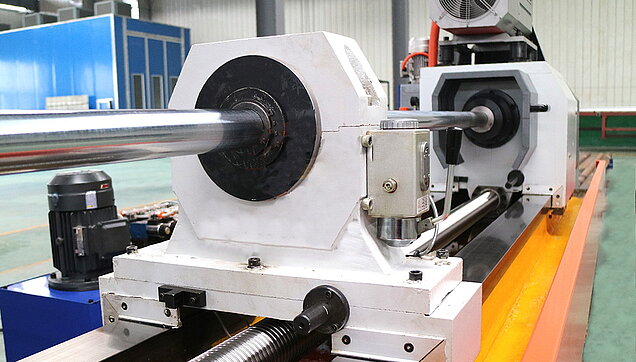
BTA Drilling Machine with Pinion and Rack feeding system
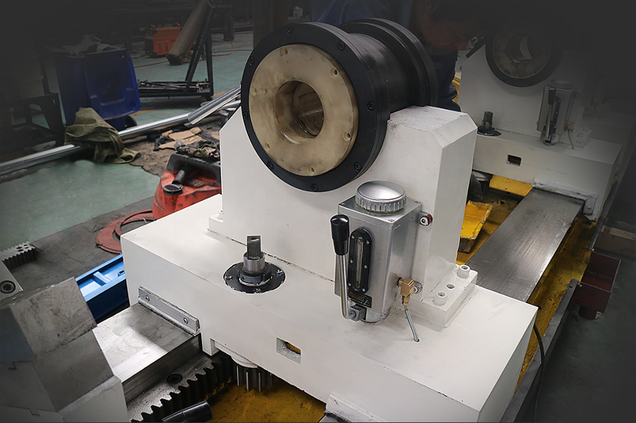
BTA drilling machines with Table
Different Table structures for great variety of parts available
Deep hole 3D BTA drilling machine with table
BTA 3D drilling and milling machines
3D BTA drilling with fixed column and T-base bed structure
Table on T-base
3D BTA drilling with moving column and fixed table
Heavy duty drilling machine
BTA Single Coordinate drilling machines with table
BTA Deep hole Drilling with big flexibility
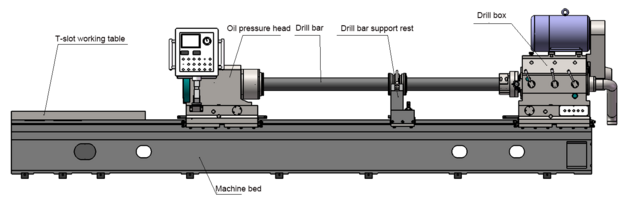
BTA Deep hole drilling with Table
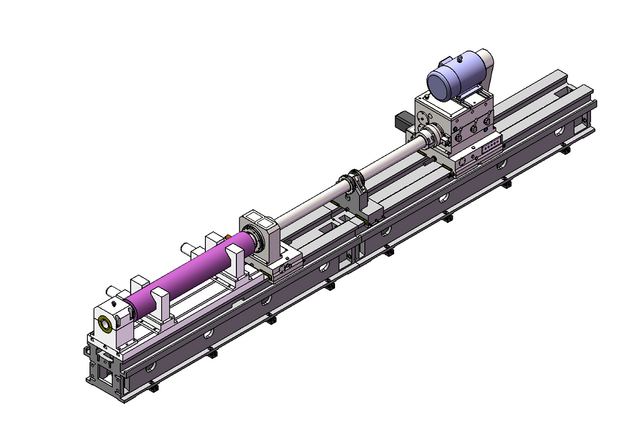
BTA Boring and counterboring with table and sub - support
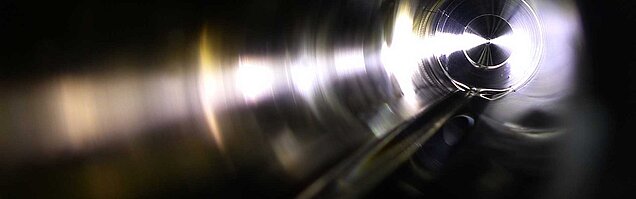